Team Leader, Active Ingredient- Central and Tank Services
Full Job Description
Description
The Team Leader, Central Services provides technical direction in Central Services according to company policy and corporate business plans. Ensures technical competence and safe work environment through proper selection and training of employees. Responsible for developing a continuous improvement philosophy within the department while maintaining compliance status (cGMP, OSHA) within the department. Implements new technologies and maintains the lowest cost of production possible. Manages the documentation flowing in/out of the production floor including, but not limited to, batch records, equipment logbooks, etc. Serves as the backup for the manager of the Department of Aerobic Antigen Production and EU Central Services as needed.As an employee of Boehringer Ingelheim, you will actively contribute to the discovery, development and delivery of our products to our patients and customers. Our global presence provides opportunity for all employees to collaborate internationally, offering visibility and opportunity to directly contribute to the companies success. We realize that our strength and competitive advantage lie with our people. We support our employees in a number of ways to foster a healthy working environment, meaningful work, diversity and inclusion, mobility, networking and work-life balance. Our competitive compensation and benefit programs reflect Boehringer Ingelheims high regard for our employees.Duties & Responsibilities
- Supervise Central Services operations and personnel to include communicating to management the status and/or progress of departmental concerns, issues, employee actions, new ideas, and all other relevant information to ensure success within the department. Hire, train, coach and develop personnel within the department in accordance with policies and procedures.
- Coordinate the activities and schedules of the department.
- Troubleshoot production problems, document findings, and implement solutions to resolve problems
- Investigate production process deviations.
- Prepare annual departmental budget and monitor departmental expenses and capital projects. Responsible for purchase of operating supplies to include recommendations new or replacement equipment. Coordination of cycle counts in the Department to control inventory in production areas.
- Manage and maintain tracking system for department key performance indicators. Provide data/metrics to Management regarding individual, equipment, production trends; provide recommendations to resolve errors.
- Accurate business function documentation management: Organize/prioritize batch record reviews as defined by Management for completed production items.
- Assist in the creation, review and approval relevant SOPs, Controlled Forms and other business function documents to support regulatory compliance, change controls and company driven initiatives.
- Endure compliance with cGMP, APHIS, OSHA, EPA, EU, and JP regulations pertaining to production process.
Requirements
- Bachelors Degree in related business or scientific field from an accredited institution.
- In addition to Bachelors degree, two (2) years of professional experience.
- In lieu of a degree, six (6) years of relevant experience.
- Experience must be inclusive of one (1) year of leadership experience.
- Experience must be inclusive of managing and auditing master receipts, batch records and process order data within relevant SAP/ERP software systems.
- Experience in ERP inventory control system(s) is preferred but not necessary.
- Experience with word processing, spreadsheets, and database management required.
- Demonstrated ability to train others and complete OJT assessments.
- Demonstrates the ability to follow systematic continuous improvement methodologies and the willingness to identify, define, and implement process improvements.
- Demonstrated knowledge of Aseptic or related production techniques and equipment.
- A working knowledge of cGMP, EU and OSHA Part 11 guidelines as they pertain to implementing process improvements on aseptic production or other production equipment.
- Must be detail oriented, able to work with minimal supervision and self-motivated to utilize resources to troubleshoot as needed.
- Ability to manage multiple on-going projects with aggressive deadlines.
- Strong proofreading skills along with excellent communication and written capabilities.
- Must be proficient in MS office applications such as Word, Excel, Outlook, etc.
- Must be able to readily learn and quickly become proficient in all software applications utilized for packaging equipment and operations.
Job Information
Job Category:
Manufacturing
Spotlight
Employer
Related jobs
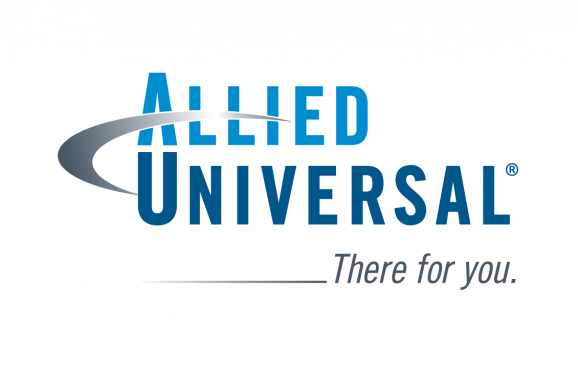
Security Guard Weekends
Allied Universal
Allied Universal, North America's leading security and facility services company, offers rewarding careers that provide you a sense of purpose. While working in a dynamic, welcoming, and collaborative...
Jun 9, 2025
Indianapolis, IN
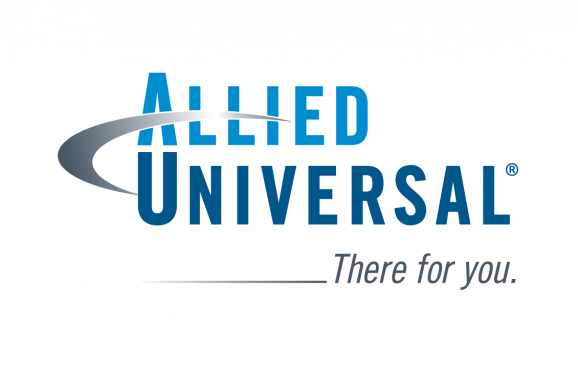
Security Guard Shopping Mall
Allied Universal
Allied Universal, North America's leading security and facility services company, offers rewarding careers that provide you a sense of purpose. While working in a dynamic, welcoming, and collaborative...
Jun 9, 2025
Los Angeles, CA
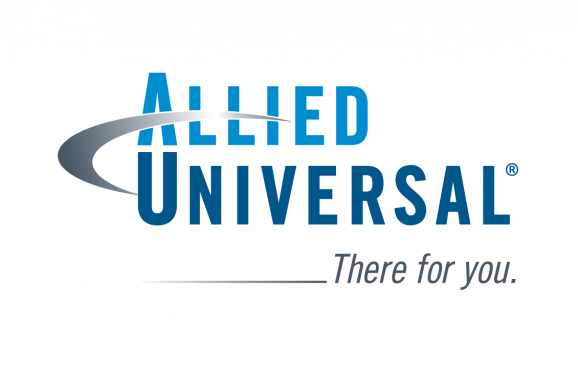
Security Guard - All Shifts
Allied Universal
Allied Universal, North America's leading security and facility services company, offers rewarding careers that provide you a sense of purpose. While working in a dynamic, welcoming, and collaborative...
Jun 9, 2025
Willard, OH